Understanding the Importance of Efficient Deutz Parts Order
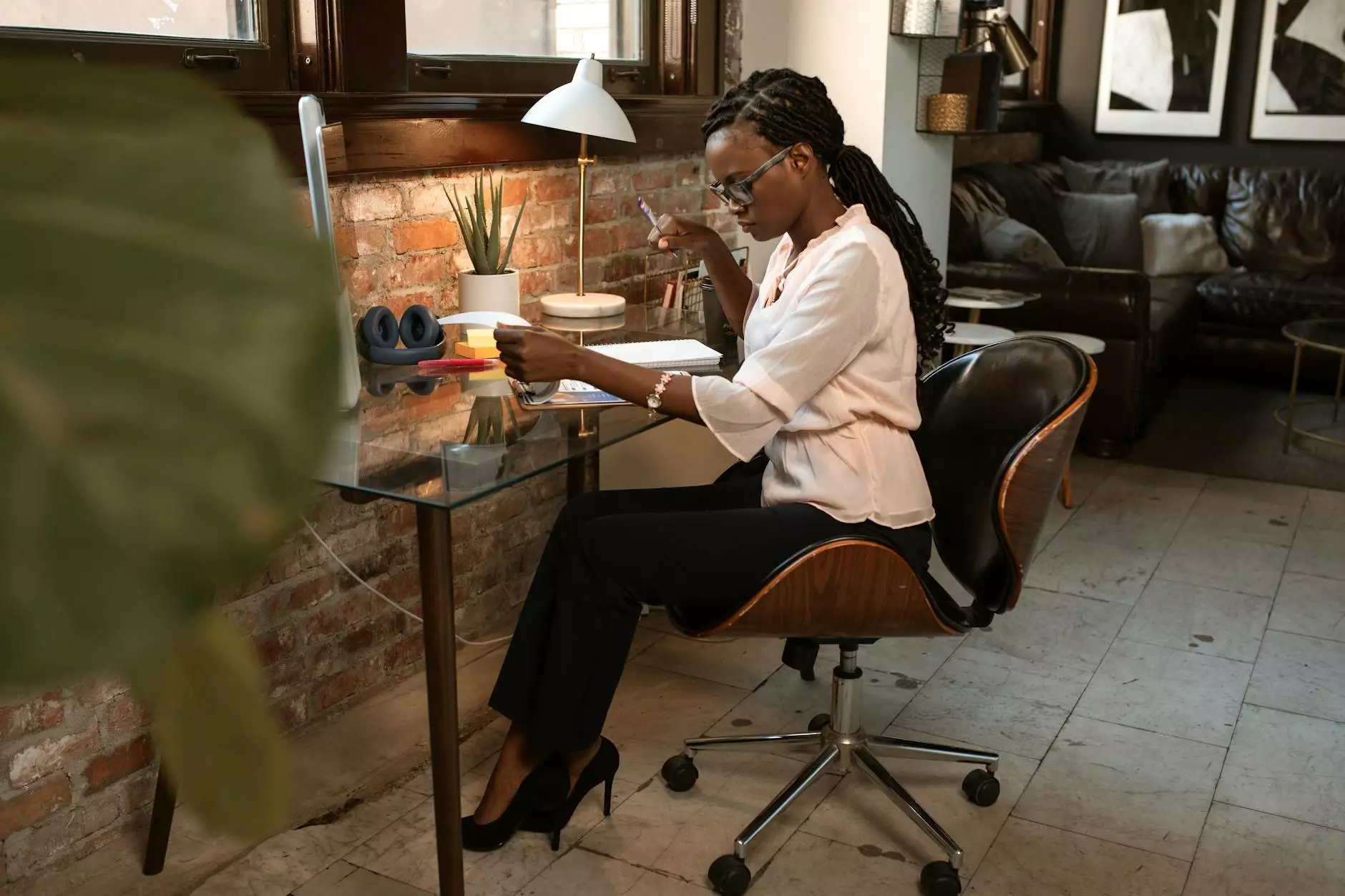
The world of diesel engineering is both intricate and demanding. A key to thriving in this environment lies in effectively managing a reliable Deutz parts order. This process is critical for businesses that rely on diesel engines, such as those in the manufacturing and power generation sectors. In this article, we will explore the significance of placing timely and accurate parts orders, and how it enhances operational efficiency, reduces downtime, and ultimately contributes to the success of companies like Engine-Family.com.
Why Deutz Parts are Essential for Your Business
Deutz engines are renowned for their reliability and performance. Whether you're operating a construction site or managing a power generation facility, having access to genuine Deutz parts is crucial. Here are some reasons why:
- Quality Assurance: Genuine Deutz parts are manufactured to stringent quality standards, ensuring optimal performance and longevity.
- Performance Optimization: Using authentic parts ensures that your engine operates efficiently, maximizing power output while minimizing fuel consumption.
- Extended Equipment Lifespan: Quality parts reduce wear and tear on your engines, thus extending their operational life.
- Aftermarket Support: Deutz offers comprehensive support for parts, including advisories and maintenance tips that enhance the product’s usability.
Streamlining Your Deutz Parts Order Process
An optimized Deutz parts order process can significantly reduce downtime and boost productivity. Here’s how to streamline your ordering system:
1. Establishing Relationships with Suppliers
Building a rapport with reliable suppliers is paramount. Working with a trusted dealer of Deutz parts, like Engine-Family.com, ensures that you have a reliable source for all your engine needs. Solid relationships allow for:
- Quick access to stock information.
- Priority service for urgent orders.
- Expert advice on the best parts for your specific engines.
2. Utilizing a Centralized Ordering System
An efficient ordering system can save time and reduce errors. Implementing centralized software allows you to:
- Track orders and inventory levels in real-time.
- Set notifications for low stock of critical parts.
- Integrate with accounting and logistics for streamlined operations.
3. Regular Maintenance and Inventory Checks
Maintaining an updated inventory can prevent unexpected downtimes. Regular checks should include:
- Assessing parts wear regularly to know when to order replacements.
- Keeping a list of fast-moving parts needed for quick access.
- Documenting order histories to forecast future needs accurately.
The Financial Impact of Efficient Parts Ordering
Cost efficiency is a primary concern for any business. A streamlined Deutz parts order process can lead to significant cost savings. Here’s how:
1. Reducing Operational Downtime
Every minute your machinery is down translates to lost revenue. Quick and accurate parts orders minimize the time spent waiting for replacements. This efficiency allows businesses to:
- Fulfill contracts and service deliveries on time.
- Maintain a steady cash flow.
- Improve customer satisfaction through reliable service.
2. Preventative Maintenance Costs
Investing in preventative maintenance and timely parts replacement reduces the risk of major repairs. The financial ripple of neglecting parts order can result in:
- Expensive emergency repairs.
- Loss of equipment value due to neglect.
- Increased insurance premiums from higher risk levels.
3. Optimizing Inventory Management
Efficient inventory management minimizes costs associated with overstocking and stockouts. By ordering parts smartly, a company can:
- Free up capital tied in excess inventory.
- Avoid rush shipping costs on emergency orders.
- Enhance negotiation power with suppliers based on consistent ordering patterns.
Case Studies: Successful Deutz Parts Order Implementation
To understand the real-world impact of efficient parts ordering, consider these examples from businesses who implemented strong ordering systems with Deutz engines.
Case Study 1: Construction Equipment Manufacturer
A leading construction equipment manufacturer faced frequent machine downtimes due to delayed parts orders. After switching to a centralized parts ordering system, they:
- Reduced machine downtime by 40%.
- Increased production output by over 30% within six months.
- Improved relationships with suppliers, resulting in better pricing and service.
Case Study 2: Power Generation Provider
A power generation provider relied on Deutz generators for electricity supply. By enhancing their parts ordering process, they were able to:
- Lower their maintenance costs by 25%.
- Achieve a 50% reduction in emergency repair needs.
- Boost overall customer satisfaction through consistent power delivery.
Conclusion: Embracing Efficient Deutz Parts Order for Success
In today’s competitive market, embracing an efficient Deutz parts order process is not just a best practice; it’s a necessity. By ensuring timely deliveries, maintaining high-quality standards, and effectively managing inventories, businesses can enhance their operational capabilities. For leaders in the diesel engine manufacturing and power generation industries, maintaining a reliable parts order system can lead to substantial gains in productivity and profitability.
Consider collaborating with industry specialists such as Engine-Family.com, who understand the nuances of Deutz parts order and can provide unparalleled support for your operational needs. With an expert partner, your business can navigate the complexities of diesel engine management seamlessly, ensuring that your operations run smoothly and efficiently.
By prioritizing the strength of your parts ordering process, you ensure not only the longevity of your equipment but also the success of your business in a demanding and evolving market.